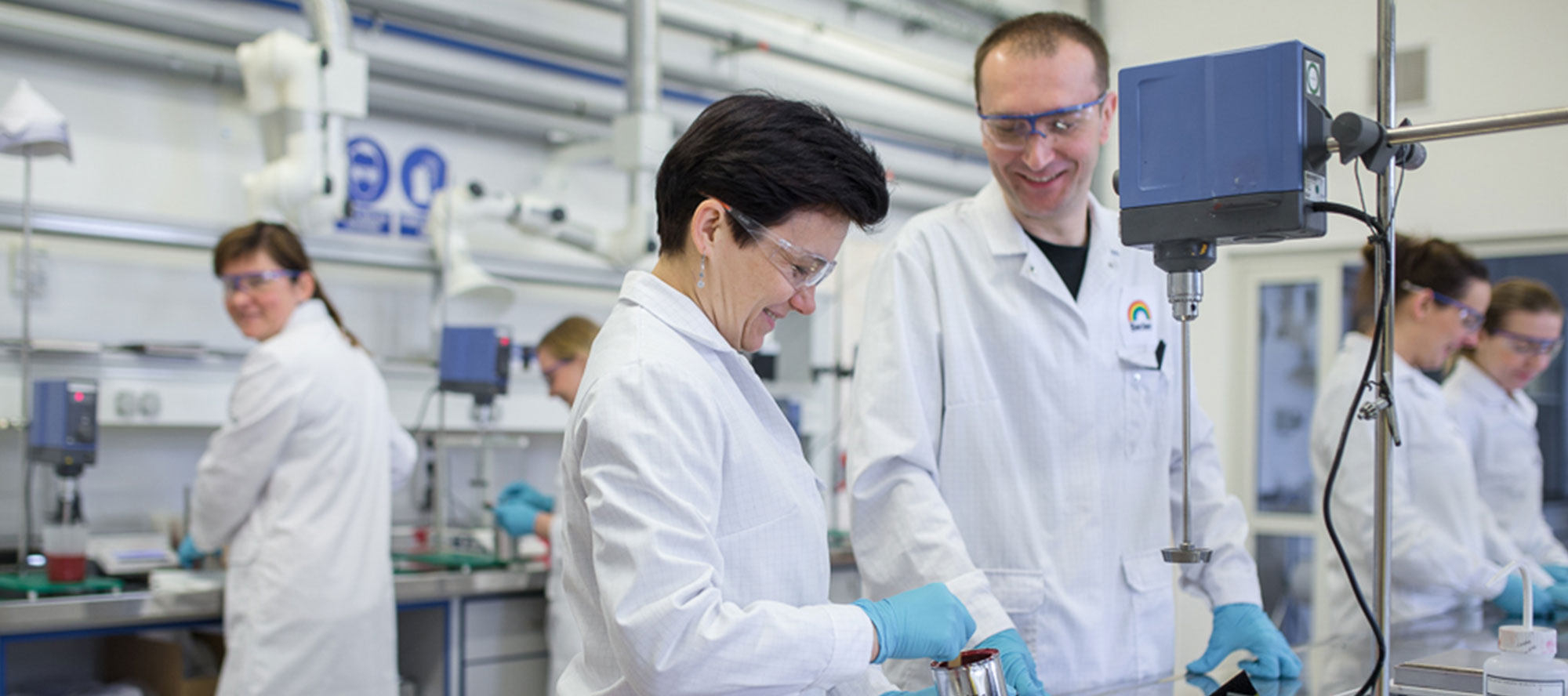
With the vision to be the most sustainable coatings company in the world, Lindéngruppen company Beckers improves the sustainability performance of its products through innovation.
Raw materials are crucial to the sustainability performance of the coatings industry as their lifecycle environmental impact is far greater than that of coating production processes. By shifting to water-based, bio-based and recycled raw materials, the industry can significantly reduce its environmental impact while moving away from linear ‘take, make and waste’ models – to more circular resource use models.
“In the coatings industry, circularity is about developing products with their entire lifecycle firmly in mind to optimise the use of resources and ensure they can be reused,” says Gavin Bown, Group Chief Technology Officer at Beckers Group. “At Beckers, we’re exploring completely new raw materials and processes to develop products based on more sustainable principles.” This includes developing coatings for customers that contain recycled content.
“By incorporating recycled plastic content into our products, for example, we can turn the problem of waste plastics into a solution,” says Bown.
However, Bown warns that the world of circularity and sustainability is littered with false economies. “We have to assess all potential solutions with Lifecycle Assessment (LCA) tools to identify and quantify the environmental impacts raw materials and processes have at different stages of the value chain,” says Bown. “Only then can we properly compare materials, understand their full impact across the value chain and choose the most sustainable.”
Beckers is working on a number of routes to decarbonise by reducing the use of petroleum-based components and replacing these with renewable and lower carbon alternatives.
“Bio-based monomers, polymer resins and solvents still produce CO2 emissions during their production, but by using plant-based input feedstocks for example, there is an inbuilt carbon capture process that acts to offset their emissions,” explains Bown. “Our immediate customers are coil coaters that have significant CO2 emissions as they use high-temperature gas-fired curing ovens that consume a lot of energy. But we can still help them reduce their emissions by providing lower carbon coatings, or coatings that enable them to consume less energy in their own manufacturing processes.”
The company is also developing alternative lower-carbon application processes together with customers, for example with low-emission 100 percent solid coatings that are applied using more efficient radiation curing processes such as ultraviolet or electron beam. Besides being more energy efficient, radiation curing technology also uses less material as around half of the coating is combusted in conventional solvent-based application methods.
“Radiation curing is a really exciting technology that we hope to launch on the market this year,” says Bown. “Greater energy efficiency and using less material significantly lowers carbon footprint.”
“To be successful, I believe that we need to look beyond our immediate coil coater customers to understand what end users in the value chain demand,” says Bown. “Focusing beyond our immediate customers in this way is key to stimulating market demand for our products.”
A product example of how Beckers meets end-user demands is its Beckry®Therm roof coating, which reduces heat absorption on building roofs. By reducing indoor temperatures by up to 10°C in warm weather, the coating promotes occupant comfort and reduces the energy needed for cooling. By maintaining a lower surface temperature, Beckry®Therm also reduces thermal tension in the metal to increase the durability and longevity of the structure.
“Beckry®Therm is a great example of the sustainability benefits our products can have for end-users downstream in our value chain,” says Bown.
Beckers has extensive in-house development capabilities but is always open to learning from other industries and partnering to develop more sustainable products and securing raw material supply.
“By looking beyond our traditional technology and materials supply base and broadening our ecosystem of partners, we can find synergies and potentially make technological breakthroughs,” says Bown. “This includes collaborating with research institutes and innovative start-up companies, and funding numerous PhDs.”
“I believe that access to sufficient quantities of bio-based raw materials will be a major challenge for industry in general in the coming years,” concludes Bown. “This is also why it’s essential that we establish good supplier partnerships today, and even consider acquiring important technology providers or suppliers to secure our access to bio-based raw materials in the future.”