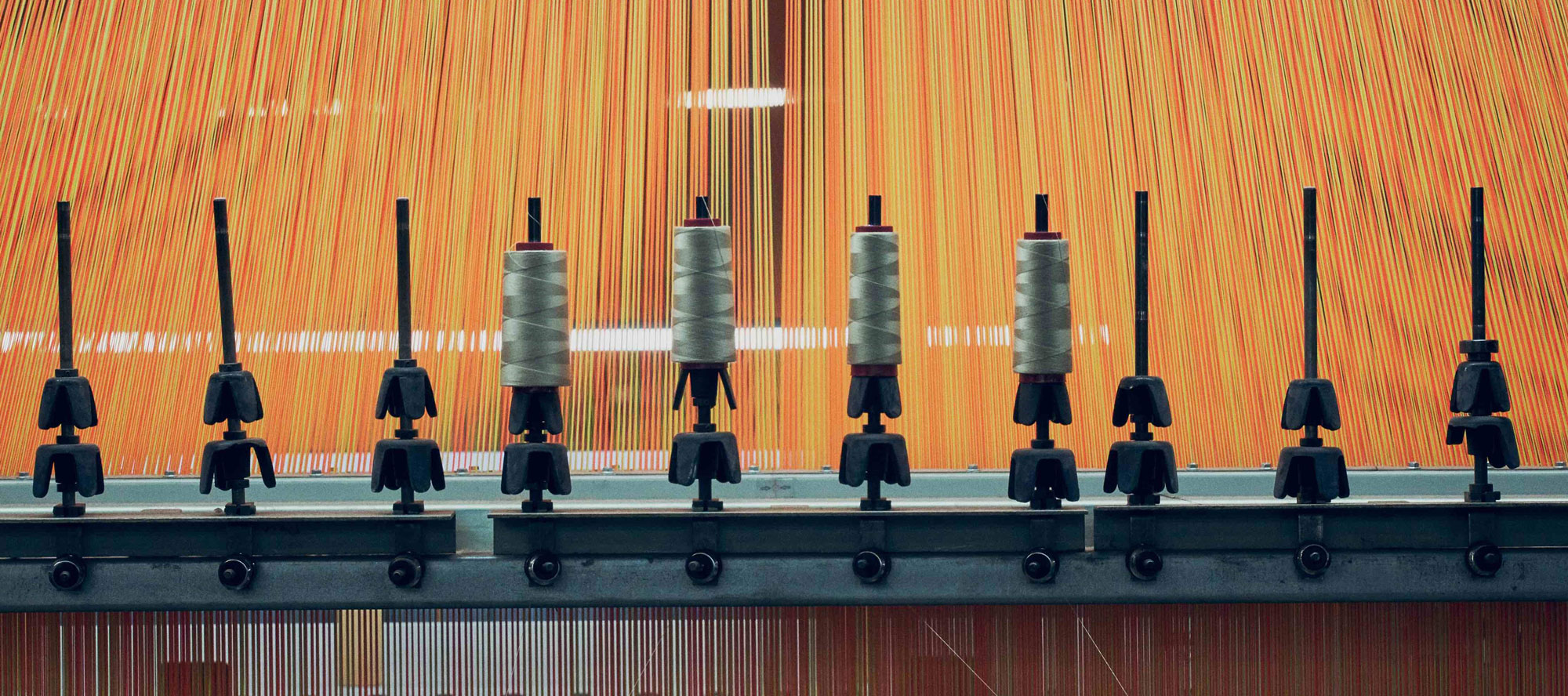
Lindéngruppen company Alex Begg have reduced their environmental footprint by switching to renewable electricity, upcycling textile waste and using less water.
Alex Begg, a leading producer of premium textiles, switched to sourcing all its electricity from renewable sources such as wind, hydro and solar in November 2022. By sourcing electricity through the UK Renewable Energy Guarantees of Origin (REGO) scheme, the company avoided generating 61 tonnes of CO2e between November and February compared with the standard UK electricity grid mix.
“We expect to annually avoid around 260 tonnes of CO2e by sourcing 100 per cent of our electricity from renewable and completely fossil-free sources,” says Fiona MacDonald, Sustainability Manager at Alex Begg. “Beyond our own business, by purchasing renewable electricity, we help to promote the demand and market for renewable electricity in the UK.”
Alex Begg’s objective is to achieve climate neutrality by 2030. This will involve overcoming some challenges, but the company is making plans.
“We are currently collecting data from our operations, business travel and shipping to more accurately map our emissions and identify where we can make savings,” explains MacDonald. “At the same time, we’re looking into various technologies and solutions that will help us on our journey to become a climate neutral business.”
“We’ve made some great progress in avoiding waste and we don’t currently send any of our textile waste to landfill or incineration,” says MacDonald. “In fact, we sell most of our production waste to two companies – Nomad Surplus Luxury textiles, who make craft packages, and also to luxury mattress manufacturer Harrison Spinks, using a small proportion of our clean textile waste as filling for their products.”
A small amount of Alex Begg’s waste textile is re-spun by a supplier that converts pre-consumer waste into yarn. Alex Begg has started buying back the yarn with around 50 per cent recycled content to trial the manufacture of different woven blankets and is currently exploring market opportunities for such products with customers.
“Only a small fraction of our waste is currently upcycled in this way, but we are looking to scale this up in 2023,” adds MacDonald. Alex Begg also donates production textile waste to universities and encourage young people to get creative with it.
Water efficiency has been another focus area where Alex Begg has made recent progress by introducing a shorter washing cycle for sample textiles that uses less water. Washing is an important part of textile processing to soften up the fibres.
“We previously used a full three-hour wash cycle for our 20-meter textile customer samples, which was the same as for our 200-meter normal bulk textile deliveries to customers,” says MacDonald. “By creating a shorter 45-minute cycle, we have saved an estimated 368,000 litres of water in these past six months alone – while reducing the amount of energy, detergent and softener we use in each sample textile wash cycle.”